Our Progress
Our Journey Of Innovation
Our strength lies in our practical solutions and close collaboration with our clients. We don’t chase trends—we engineer to solve real problems. And every year, we move forward.
Innovation at Portsmouth Plastics is about finding better ways to serve, support, and simplify. Our machines work hard, last long, and evolve with our customers. We understand that when a client receives a new machine, it’s not just about the machine itself—it’s about the entire experience. That’s why we offer personalized commissioning services to guarantee the proper operation of the machine and its seamless integration into the client’s existing production process. Every function, every feature, would meet the unique requirements of each client, delivering the efficiency, durability, and ease of use they needed to thrive in their industries.
From our early years producing basic blow moulding units to today’s more refined injection blow moulding machines, our journey has been one of purposeful improvement, driven by practical innovation rather than flashy claims. While others in our industry have made global headlines, we’ve focused on refining what we do best—delivering reliable, user-friendly machines tailored to production floors.
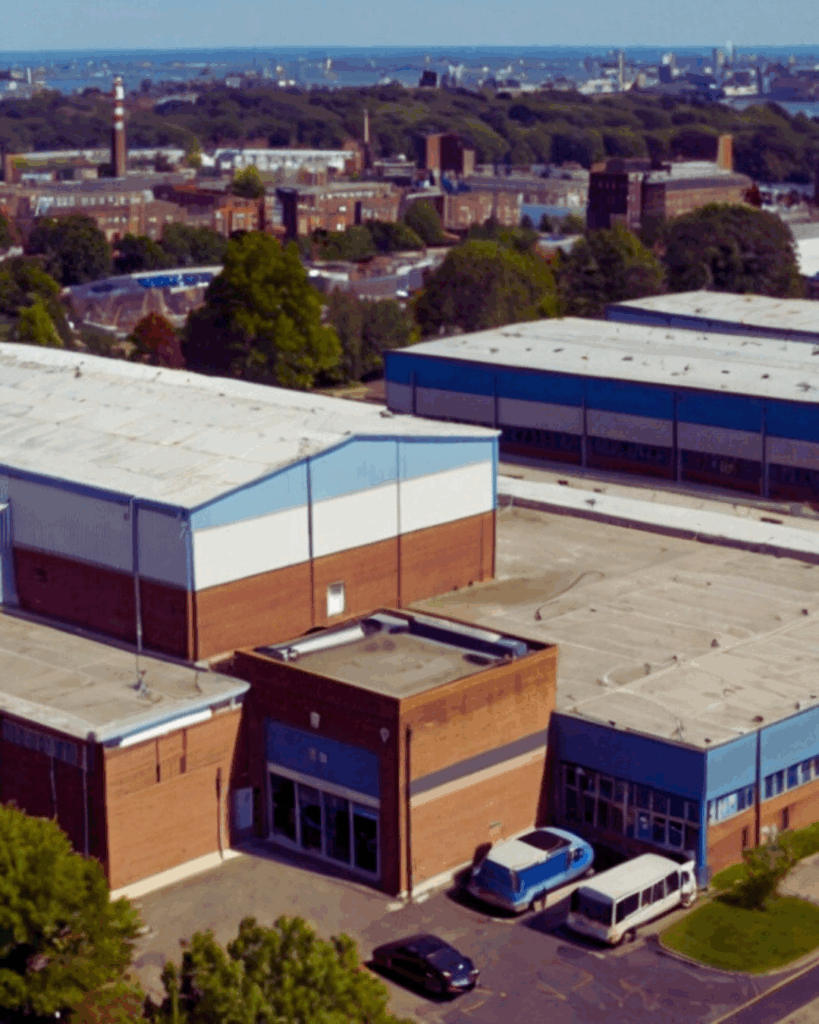
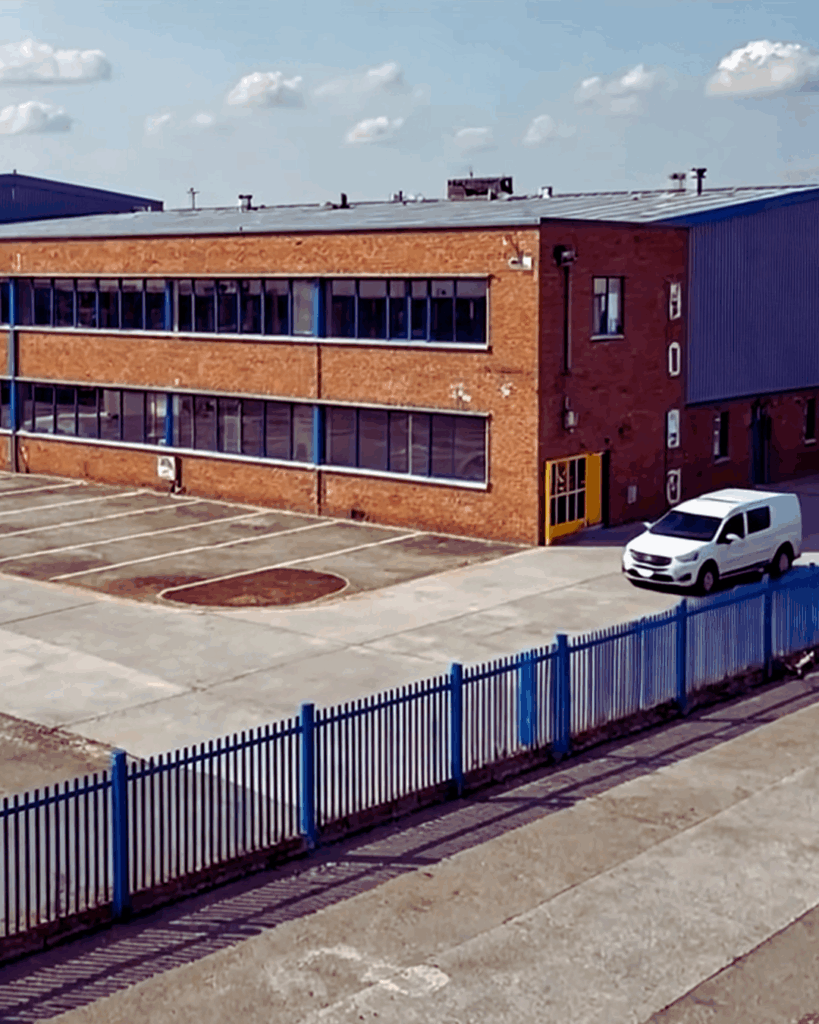
We're Proud To Have
- Improved our injection blow moulding cycle times by over 30% in the past five years
- Expanded our product line with machines capable of handling both small and medium volume applications
- Built strong, long-term relationships with UK manufacturers and growing international partners
- Reduced our machine energy consumption through efficient heating and simplified control systems
- Maintained consistent after-sales support and machine lifecycle assistance for every client we’ve partnered with
Manufactured With Accountability
At Portsmouth Plastics, every machine is built with one principle in mind: nothing leaves our floor unless it meets our full approval. Before a machine reaches our clients, it goes through a rigorous process of testing, adjustment, and validation — because performance in the field starts with precision in the workshop. We assess the machines based on how they perform and our focus is on what they can handle under real pressure, in real working conditions. That means pushing each system through multiple phases of technical evaluation, simulating the kind of demands our clients will place on it over years of operation.
To make sure every machine is ready, we carry out:
- Comprehensive quality control — checking every function, motion, and interface for consistency and reliability.
- Material testing — inspecting key parts for strength, resilience, and structural integrity .
- Durability trials — simulating long-term wear through continuous workload stress to ensure lasting performance.
- Commissioning calibration — fine-tuning the machine to the customer’s specific production needs before handover.
Technical Support and Operational Reliability
At Portsmouth Plastics, we provide comprehensive setup instructions, operational training, and ongoing technical support as standard with every machine. Our team ensures that each unit is installed correctly, optimised for the customer’s production environment, and ready for full-scale operation from day one. Customers regularly tell us that what sets us apart isn’t just the machines themselves, but the level of aftercare and technical reliability we offer throughout the lifecycle of the equipment. Our injection blow moulding machines are developed with a clear focus on reducing variability in production, streamlining changeovers, and minimising downtime. We engineer our systems to deliver repeatable performance and improved output consistency across a wide range of plastic container applications. Every unit we produce follows a standardised build process based on proven mechanical principles, precision components, and adherence to strict quality control procedures. Our machines are tested under load and evaluated against defined performance benchmarks before being dispatched.